Success Stories
"A multinational operator was experiencing production issues on a single oil well, and the cost to continue injecting at the current rate and the cost of the rental compressor was not economical. After creating a survey report for the well to identify the flowing tubing pressure/temperature profile, an ALTEC technician worked up a rig design with new mandrels and added ABBA Pilot valves allowing the operator to reduce the injection rate from 500 mscfd to 150 mscfd, eliminate a costly rental compressor, and ultimately increase oil production from 127 BOPD to 233 BOPD.
Detailed Explanation: ALTEC ran a survey to identify the flowing tubing pressure/temperature profile for the new install. The RIH and POOH profiles show cooling the bottom valve, confirmed by the change in tubing flowing pressure gradient. The fluid level in the casing is at the orifice valve which indicates that gas was being injected through the orifice at one time. Once the tubing installation was completed by an ALTEC technician, he kicked the well off with the ABBA pilot valve installed and the injection rate was drastically reduced."
Download Supporting Material
"A Permian operator’s well production dropped from 350 BFPD to 167 BFPD after an offset frac in the Permian Basin. They suspected the decline was due to a bad gas lift valve. An ALTEC lift expert performed a flowing gradient survey that exposed the actual reason for the lower production was due to restricted inflow, not a thief valve, which saved operator between $60K and $80K, had they done a workover.
Detailed Explanation: The survey running in the hole profile showed that gas was being injected through the three valves above orifice valve on the bottom. This was confirmed by pulling out of the hole profile. Most of the injection gas was entering through the valve just above the orifice valve, and it was determined that the two valves above were passing injection gas due to over injection. Even though the downhole flowing tubing pressure was lower than the downhole injection gas pressure at the orifice, there was no gas being injected, so it appeared that the orifice valve was plugged. The fluid level shot showed the casing fluid level to be at the orifice valve, which means at one time the injection gas was entering through the orifice valve. The bottom hole pressure at the packer measured 874 PSI, which calculated to be an extrapolated pressure of 990 PSI at the mid perforations. The results from the flowing survey showed that there was an issue with a plugged orifice valve, but the main reason there was a drop in production was due to restricted flow from the reservoir, which was likely caused by the offset frac."
Download Supporting Material
Operator increases production by 28 BOPD in a well by upgrading standard IPO valves with
valve technology from ALTEC.
A major operating company in the Permian wanted to increase output by switching from a traditional IPO valve to ALTEC’s proprietary Constant Flow® valve. The increase in production rates are illustrated below in the two charts.
Download Supporting Material
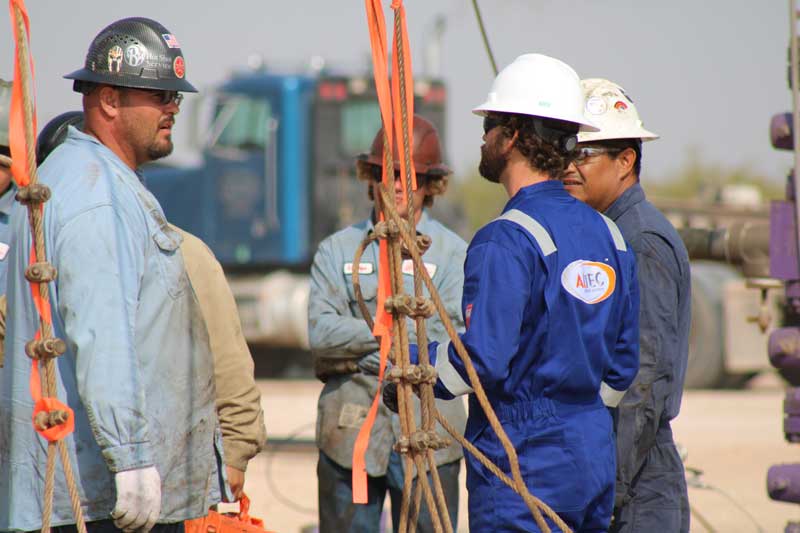
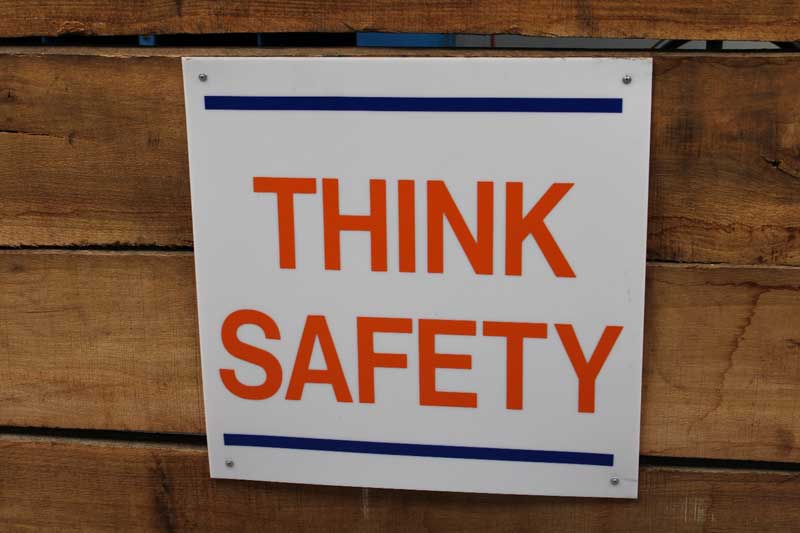
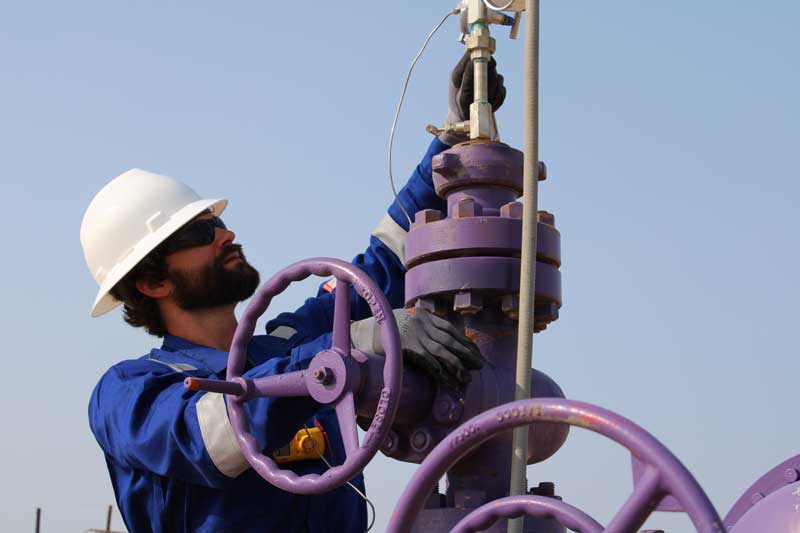